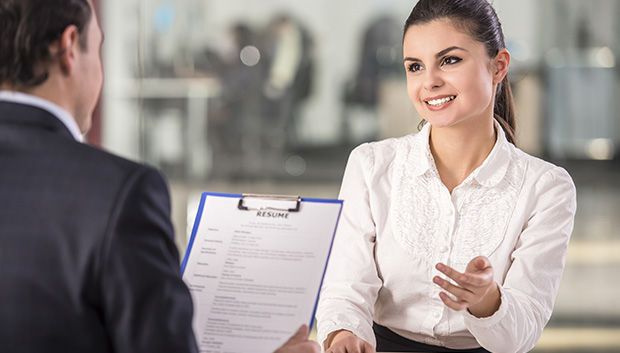
The following is a list of currently available employment opportunities with Utah Medical Products, Inc.®. UTMD is actively seeking individuals to fill these positions and encourages those who qualify to submit their application.
To apply for one of these positions, see the How To Apply page for instruction on sending in your resume and cover letter.
Please submit your resume and cover letter to careers@utahmed.com. If none of these positions match what you are looking for, you may still submit your resume and cover letter. Your information will be kept in the UTMD human resource database. The next time a position opens up, UTMD looks for potential matches in this file before beginning a wider search.
You are also encouraged to return to this page often, since the listing is continually updated.
OPEN POSITIONS
- Injection Molding Process Technician - Midvale, Utah
Job Description / Primary Functions:
1. Responsible for the efficient set-up and operation of silicone and thermoplastic injection molding machines (including auxiliary equipment) for the production of precision molded components. Trouble-shoot and determine root causes quality/part issues. Change inserts and cores as required.
2. Mold processing and process troubleshooting of various types of injection molding and extrusion equipment to ensure optimum quality of parts produced.
3.
Ensure that correct materials and procedures are utilized, and that room organization and cleanliness is maintained.
4.
Train molding operators in the safe operation of machines and equipment.
5.
Execute daily tasks in accordance with production schedule.
6. Identify and recommend improvements to molds and equipment.
7. Work with the Quality and Engineering departments to maintain and improve process control.
8.
Assist Engineering in validation of new tools and testing of repaired tools.
9.
Perform other related duties and tasks as assigned by operations management.
Qualifications and Requirements:
1. Mechanical aptitude and working knowledge of plastic and silicone rubber injection molding machines and auxiliary equipment.
2. Ability to understand a variety of instructions, including mechanical drawings.
3.
Good communication skills and a positive attitude with coworkers.
4.
Compliance with the Company’s Code of Conduct, including a work ethic consistent with all Company policies.
5.
Basic computer skills (spreadsheets, word processing, etc.).
Education:
1. High school diploma or equivalent.
2. 2-year technical degree preferred.
Full time with excellent benefits, $20 - $26/hr depending on experience. Part time without benefits, $22 - $30/hr.
* * UTMD is an Equal Opportunity Employer * *